chickenStripCharlie
Coast to Coast
Hi guys,
Does anyone know the purpose of this part on a 93 honda nighthawk wheel?
Part #6 below. It is pressed into a 20mm ID bearing (on the cush drive) to turn that bearing to 17mm ID. I am not able to figure out why they wouldn't have just used a 17mm ID bearing like they did for the other two wheel bearings.
Can someone explain it to me? It protrudes out of the bearing some 5mm or so. Is this just to help with axle alignment when sliding the axle in ... to take up that gap between the wheel bearing and cush bearing, or what?
I'm swapping this 93 wheel onto my 83 and was just going to get new bearings that are same OD but 20mm ID to accept '83 axle. Then i noticed that part on the cush bearing.
Does anyone know the purpose of this part on a 93 honda nighthawk wheel?
Part #6 below. It is pressed into a 20mm ID bearing (on the cush drive) to turn that bearing to 17mm ID. I am not able to figure out why they wouldn't have just used a 17mm ID bearing like they did for the other two wheel bearings.
Can someone explain it to me? It protrudes out of the bearing some 5mm or so. Is this just to help with axle alignment when sliding the axle in ... to take up that gap between the wheel bearing and cush bearing, or what?
I'm swapping this 93 wheel onto my 83 and was just going to get new bearings that are same OD but 20mm ID to accept '83 axle. Then i noticed that part on the cush bearing.
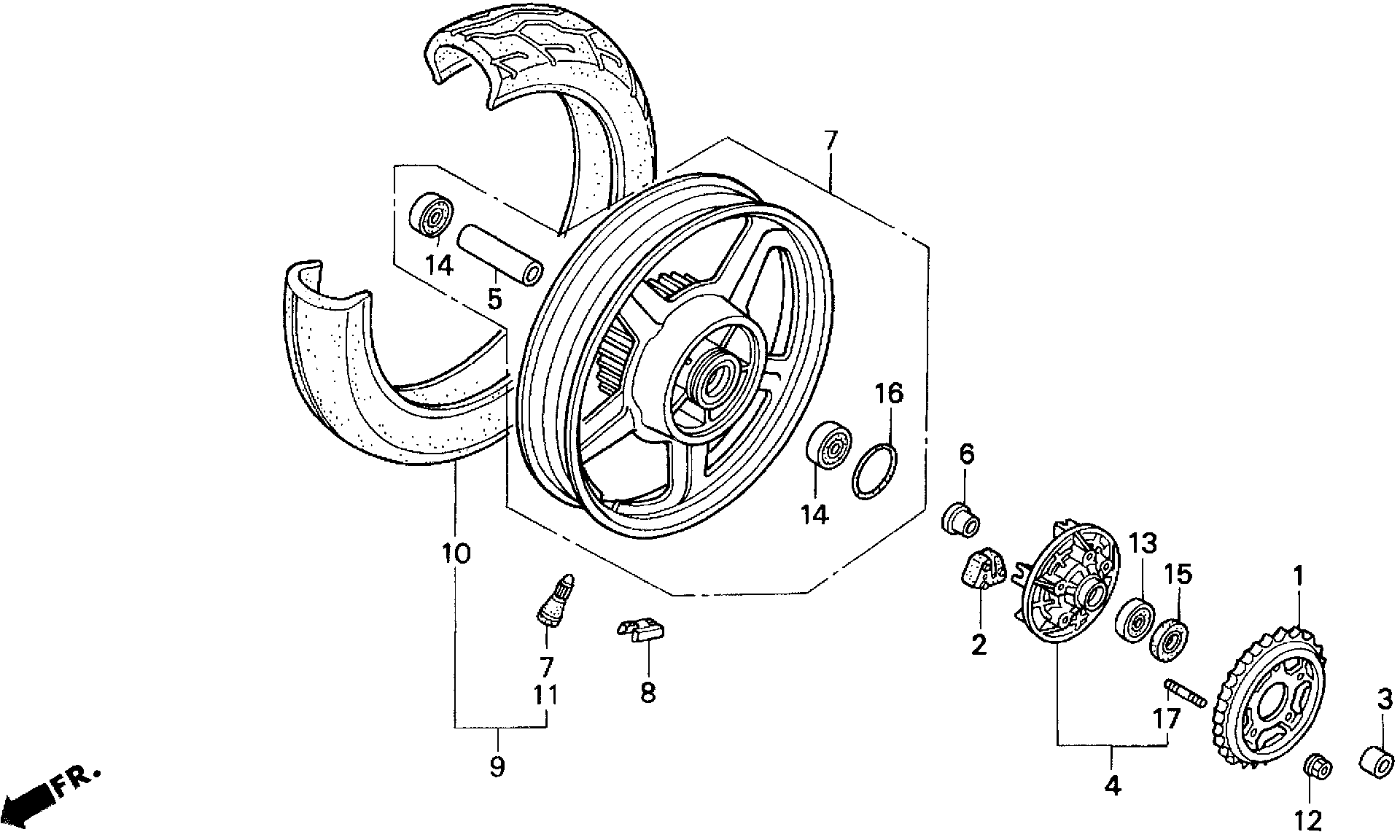
