hurco550 said:
not to threadjack man, but im about to pick up a south bend 9" here soon, and im digging your setup. Could you give me any more info on it? treadmill motor?
Sure. No problem.
1. I found an Avanti treadmill going cheap on eBay. 99c auction as the motor was making horrible noises. Turns out 2 new bearings and a new set of brushes and it worked perfectly, was also a 2.5HP peak HP motor so plenty more than you would need for a 9" lathe (fortunately the flat belt slips before things get too out of control). I took the motor mount and welded it to a plate for attaching to the lathe motor mount. Plate had elongated holes for adjustment:
Next I bought a pulley from my local bearing shop and opened up the ID to accept the bushing on the end of the motor. The motor was designed to run the opposite way so I had to loctite the bush to the motor as it was on a reverse thread:
Originally there was a fan on the end of the motor, but because I had reversed the motor it would pull air through it vs pushing. So I bought a fan, fan housing off eBay and made a bracket to connect it to:
The motor was terminated on a high end 10A audio connector which gave me a quick release. Did the same thing with a cheap magnet RPM sensor. I did this for the control box so it was easy to separate all the items vs having it all connected. The things on the left and right are just foam covered holes for ventilation:
I was worried about cooking the DC motor controller in the control box, so the foam covered holes allowed air to enter and fresh air was pulled through via this fan on the top. The fan is run off the 12V RPM sensor wiring so it all comes on together to keep things simple:
The control box basically has 240V power and 12V power feeds on the left hand side, on connectors so easily removed. Motor and RPM sensor connectors on the bottom. The box contains a KB Electronics DC motor controller with an additional heat sink with fins in the same direction as the air flow from the fan on top. I have an emergency stop button in series with an LED switch for main power, a black rotating switch to activate the motor, potentiometer for speed control and the RPM dashboard with a switch next to it to turn it (and the fan) on/off:
The RPM sensor was attached by bending up a small piece of Alu:
It reads off a magnet which I drilled a hole in my 3 jaw chuck and epoxied in the magnet:
An eBay job extraordinaire but it works perfectly. The adjustment on the dial works right down to 40 RPM so I almost never change the belts. Only thing I do sometimes is put it in back gear and lowest ratio for tapping or really slow work.
For those wanting a more stripped down view on the build here is inside the control box. It looks like a few wires but in essence it is very simple. You can see the DC controller (red part) is quite small actually. However the control box was sized off the heat sink it is attached to. Probably overkill from my end, especially with the fans etc, but better too much cooling than too little:
The wire for the black rotating motor switch is not connected here as the cable is a bit short with the door open. This view is so you can see the stuff in the door too. Box is hinged with a high tech sticky tape hinge

:
Here is how it looks when it's running (although not under its own power, I just turned the chuck by hand):
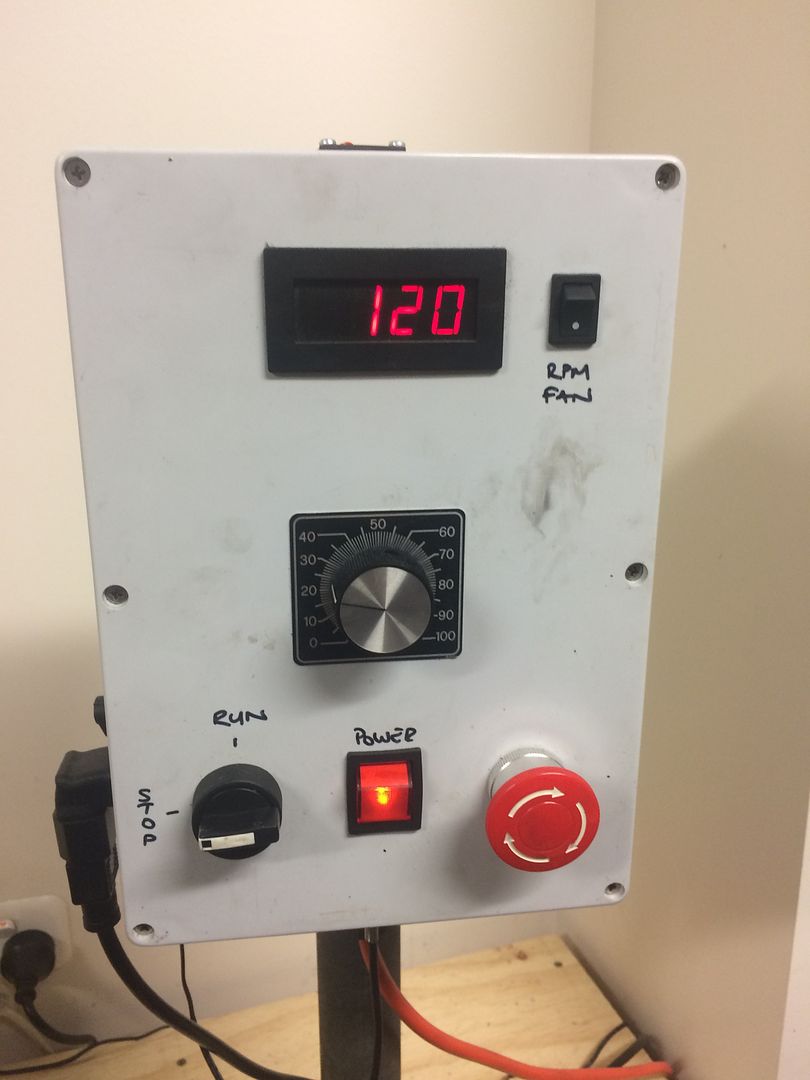