neevo
Over 1,000 Posts
I've been on the lookout for a lathe for ages, but the prices were just too high (approx $800) and so I pretty much gave up on the idea. However Lady Luck showed me a 24hr eBay listing and I jumped on it, even if it turned out to be a dud, I was sure I could at least make my money back as it only cost me $320. Reason for the thread is I want to work out a) how this thing works b) how I can check its in working order and look to repair/replace any bits that need attention.
Here it is in all its glory:

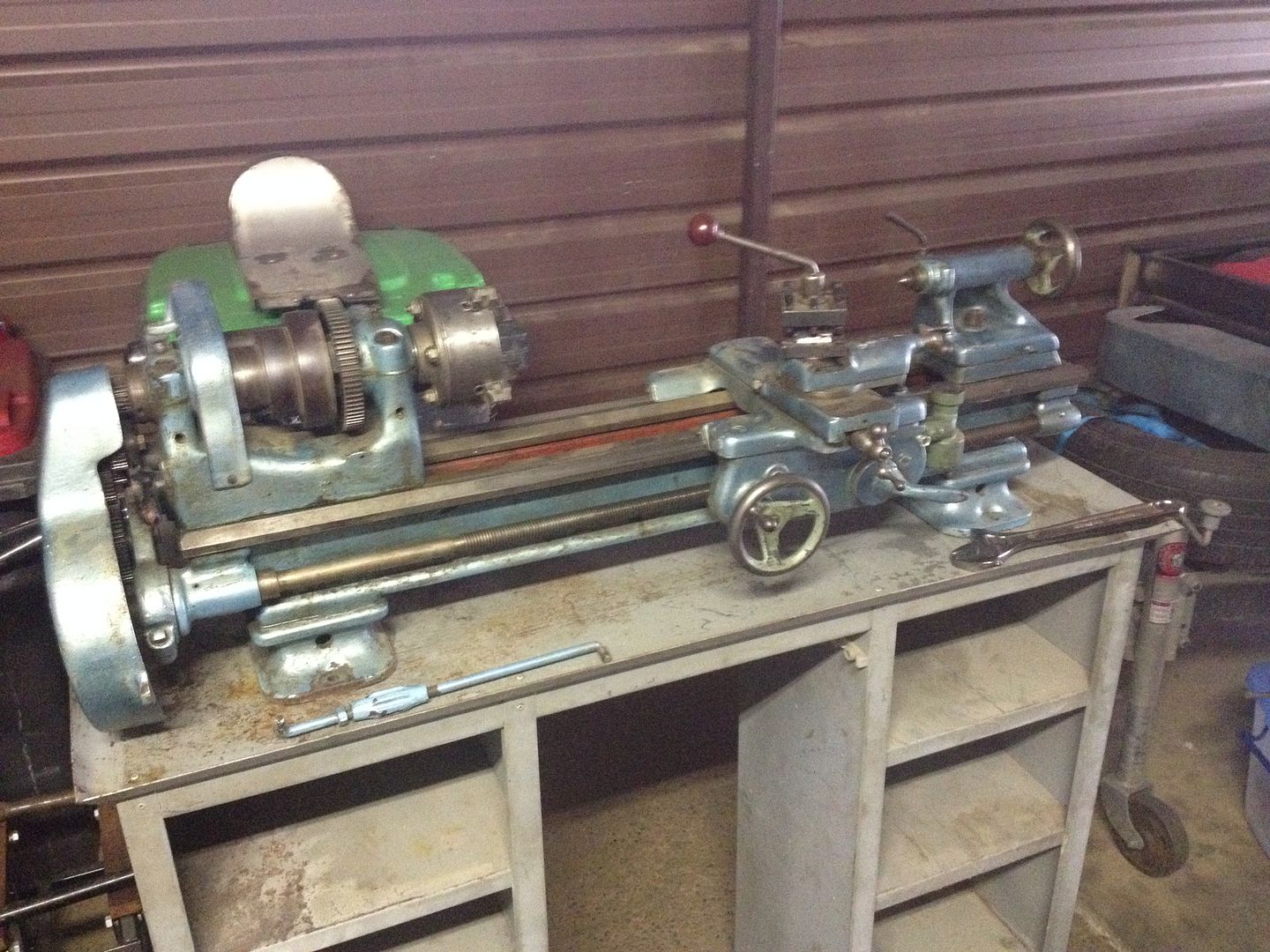
The motor was attached to the stand in a way that I need to double check to make sure its suitable. Looking online it looks like the Hercus lathe has this motor attached separately to the bench in a way that is far enough away to allow tensioning of the belts. Here is the motor:
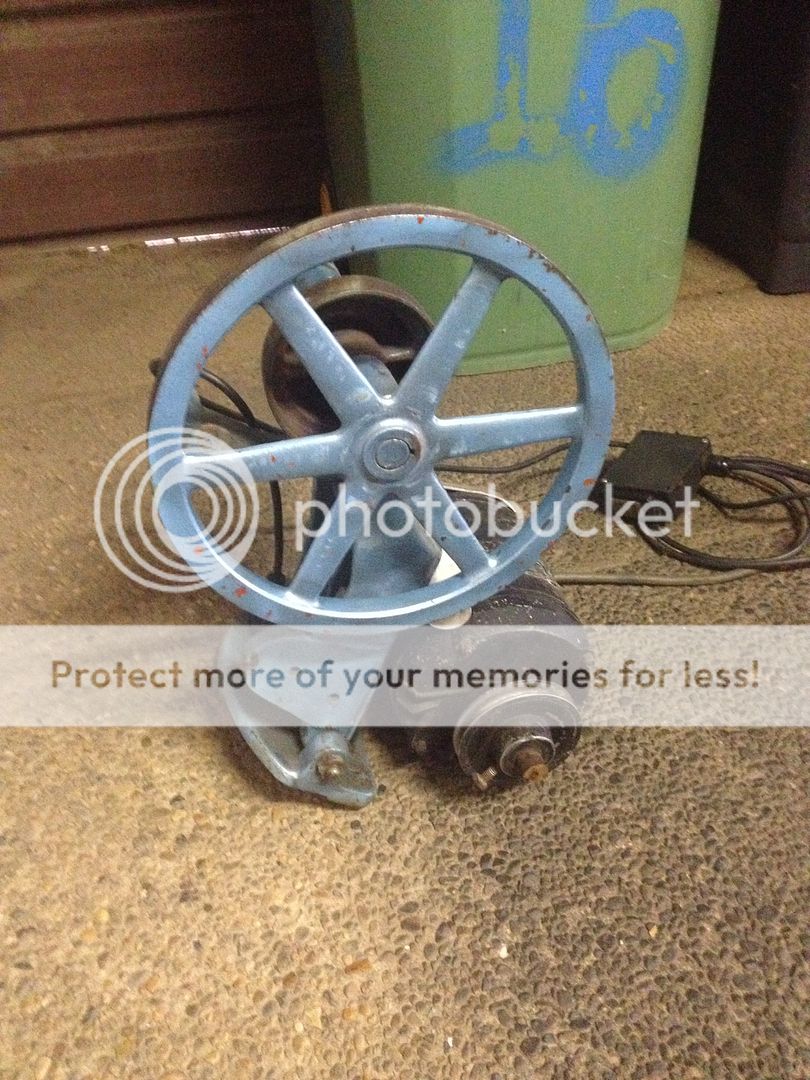
So what help do I need?
1. Any pointers on how this thing works or even pointing to a manual would be fantastic
2. What should I look to do to clean this thing up? What should I check to make sure its in good condition (straightness or wobblyness)
3. The motor is pretty rough so I am thinking of replacing it, can I swap it out for a direct drive model instead or should I just replace the motor and keep the belts?
4. The belts are buggered. Where can I get replacements?
Thanks in advance.
Here it is in all its glory:

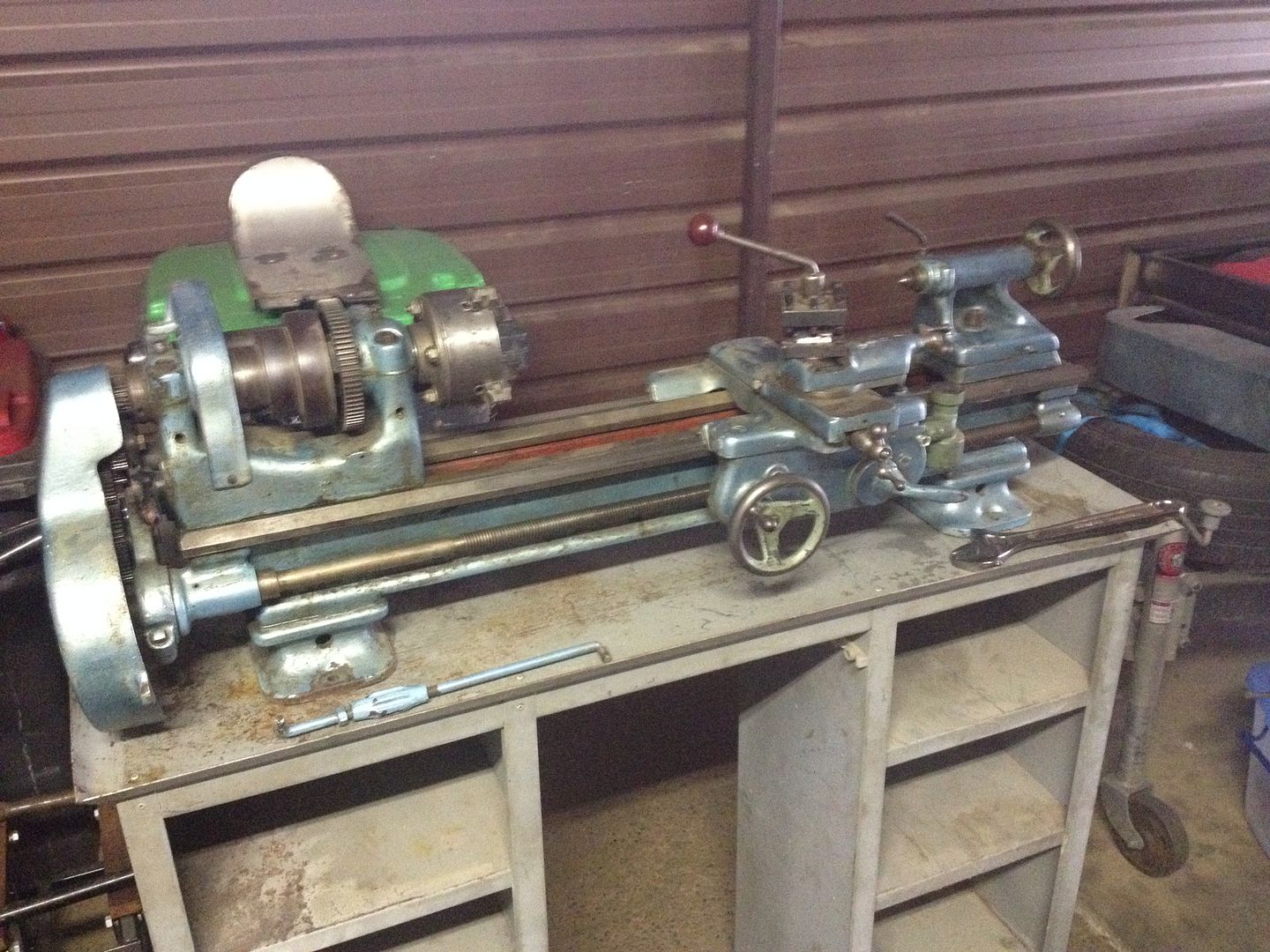
The motor was attached to the stand in a way that I need to double check to make sure its suitable. Looking online it looks like the Hercus lathe has this motor attached separately to the bench in a way that is far enough away to allow tensioning of the belts. Here is the motor:
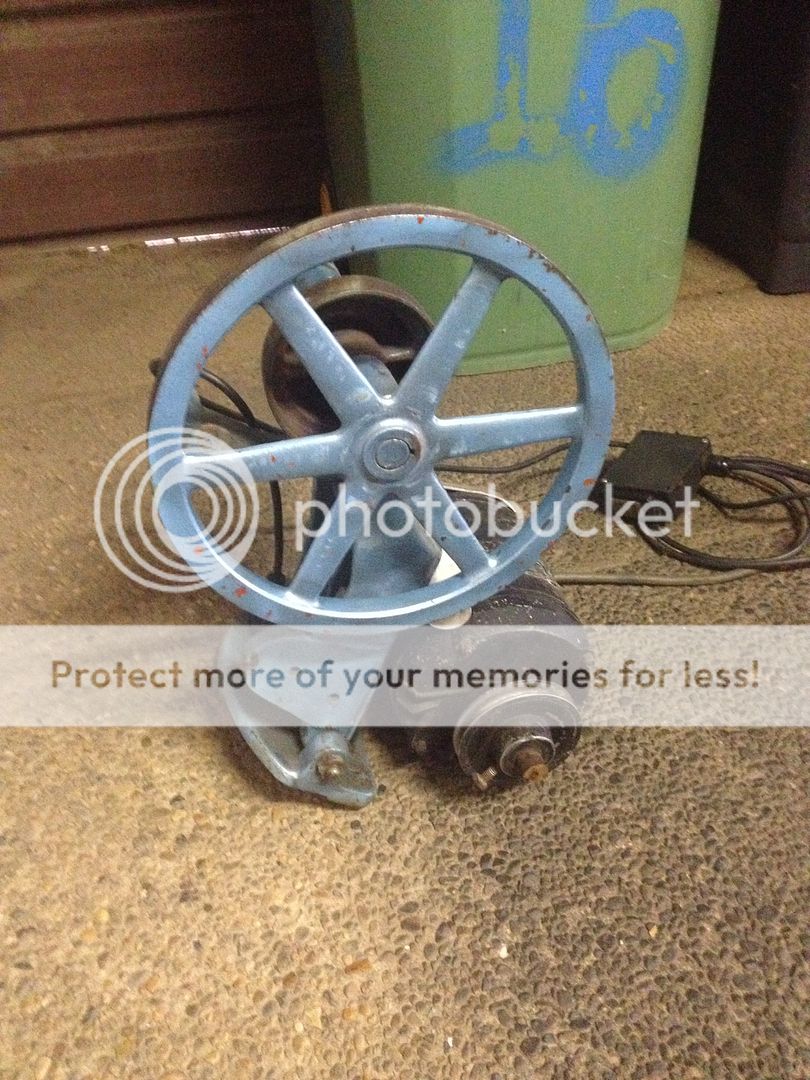
So what help do I need?
1. Any pointers on how this thing works or even pointing to a manual would be fantastic
2. What should I look to do to clean this thing up? What should I check to make sure its in good condition (straightness or wobblyness)
3. The motor is pretty rough so I am thinking of replacing it, can I swap it out for a direct drive model instead or should I just replace the motor and keep the belts?
4. The belts are buggered. Where can I get replacements?
Thanks in advance.